A Quiet Revolution in Aircraft Maintenance
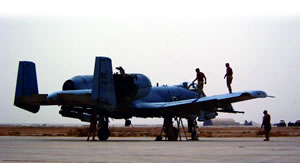
The handheld digital revolution is gaining ground with maintenance teams worldwide.
By Patrick Chisholm
The need to be global, mobile and deployable applies just as
much to aircraft maintenance capabilities as it does to the aircraft itself.
And in recent years, the process of repairing and maintaining military aircraft
has become dramatically more global, mobile and deployable thanks to portable
maintenance aids (PMAs) and electronic technical manuals (ETMs).
Maintenance technicians are not necessarily turning wrenches
faster - the difference is that they are getting information much faster, thanks
to e-tools. PMAs and electronic documentation allow the technician - whether on
the flightline, in a hangar, depot or office - to perform tasks without leaving
the duty location.
Surprisingly, aircraft mechanics spend as much as 40 percent
to 50 percent of their time looking for information. The more complex the
equipment, the more time they typically have to spend on research. The key is
to reduce that research in order to have the maintainers focus on what they are
paid to do - and above all, to improve the readiness and effectiveness of U.S.
air power. "The faster you can get them the information that is relevant for
the problem they are trying to solve, the more efficient or productive they are
going to be," said John Snow, vice president of marketing and business
development for Enigma Inc., Burlington, MA.
Thanks to advances in computing speed, storage, voice
recognition, miniaturization and wireless communications throughout the Air
Force - as well as in the other services - maintenance technical data is gradually
being converted from paper into ETMs, and the use of manual documentation is
gradually being converted to electronic means. Going hand-in-hand with that
change is the growing use of PMAs.
Aircraft with digitized technical data include the F/A-22,
CV-22, C-17, B-52 and the next-generation Joint Strike Fighter. All technical
data for new aircraft, and almost all data for engines, have been digitized.
Some older aircraft have digitized data as well. However, most of the
latter - particularly those potentially going out of the inventory - often lack
such digitalization. "Economically it might not make sense to digitize that
tech data because there is a cost there. But data for all of our new aircraft
and equipment are digitized," said Lieutenant Colonel Mack Breeland, chief of
the Air Force's Maintenance Information Systems cell at the Pentagon.
Types of digitized documentation involved may include task
cards, inventories, mechanical drawings, technical orders, maintenance manuals,
parts illustrations, service bulletins, job guides, fault isolation manuals,
illustrated parts breakdowns, structural repair manuals and inspection work
cards. Basically, anything that currently exists in technical data format can
be transferred to electronic format.
While desktop computers cannot be used at the flight line, PMAs
can. These are mobile e-tools used at the point of maintenance, typically
taking the form of a ruggedized laptop computer or a handheld device.
The Air Force began studying PMAs in the early 1990s and
started using some devices in the mid-1990s. But it only has been within the
last few years that PMAs have become more common.
Under the Integrated Maintenance Data System, all logistics
information components will be integrated into a single, Air Force-wide
maintenance information system, providing technicians with software, hardware
and infrastructure solutions at the point of maintenance, while also providing
integrated capabilities across the entire maintenance enterprise.
One E-Tool for the Job
PMAs enable four basic capabilities: to open and close work
orders; to order parts; to track parts through the system (thanks to automatic
identification technology or AIT); and to access and view technical data. They
also can be used to perform advanced diagnostics and interact with experts at
remote locations.
"Those are the four pieces we are trying to put on the one
e-tool for a job," said Breeland. "We don't want our technician to have a
computer for documenting the maintenance, a computer to order the parts, a
scanner to read the barcode label, and then one to do the tech data. We want
all that on one e-tool. That's what point of maintenance is."
PMAs are typically small instruments but can be large as
well, weighing up to 25 pounds. They range from inexpensive commercial
off-the-shelf (COTS) devices to ruggedized units customized for military use,
which can cost as much as $20,000. Generally, PMA hardware takes two forms:
"thin-client" and "thick-client" devices. The thin devices contain very little
memory, but can be updated frequently. Thick-client PMAs are larger, containing
memory and more processing power.
Depending on the type of PMA, the Air Force has used various
brands. For hand-held terminals, they include Intermec and Symbol. For ruggedized
laptop computers, Itronix and the Panasonic ToughBook are common brands. The
Air Force's air logistics centers are commonly using Fujitsu. The Air Force
also has tested Xybernaut wearable computers, which are worn on a vest or a
belt.
There are many other products as well, including DataTrak
products, Sanders' Enhanced Diagnostic Aid (EDNA), the Walkabout Hammerhead,
AMREL Rocky Patriot III ruggedized notebooks, Compaq & Palm handheld
devices, and the Dolch NotePAC II.
There is also the CROC - compact ruggedized operational
computer - manufactured by Tactronics, Westhampton Beach, NY. It was originally
designed for special operations, but Tactronics found that it is conducive to
maintenance environments as well. "A lot of the same reasons why the special
ops guys want that laptop are extremely germane to other people, like
maintenance technicians, who have to operate in rugged environments - where
there's dust, dirt, rain, and those kinds of things," said Bill Silhan,
president of Tactronics. The CROC, he says, is also useful in bright sunlight,
thanks to a special optically bonding coverglass to the display.
Tactronics also makes the Tri-Sector Access Point, enabling
portable Wi-Fi networks that can be placed in hangers or elsewhere where maintenance
technicians operate, giving them connectivity to the central server. "They
access the main database with a laptop and the schematics come up locally on
the laptop," said Silhan.
One type of wearable computer projects what is on the screen
onto the inside of one's glasses, letting a technician read instructions while
performing a repair, freeing up both hands to do the work. This technology was
tested at Hurlburt Field and Tinker AFB. However, Breeland said sunlight and
other factors reduced the practicality of the product.
PMAs improve data accuracy and speed of information flow by
doing it at the point of maintenance versus waiting to subsequently document.
The information is automatically fed into a database. The Air Mobility Command
(AMC) has phased in other functions to include links to the illustrated parts
breakdown and quick reference list, as well as e-mail access through the local
intranet. In cases where a wireless LAN is being used, the data is immediately
transferred to the main database, improving data speed and accuracy.
"In addition to the standalone PMA out in the field that
helps with productivity and efficiency, data can be sent back to a central
mainframe server or a cluster of client/server servers and really help in
knowledge management," said Mike Binko, director of communications for Xybernaut,
Fairfax, VA. "So it's a symmetrical data flow - not just taking data out into
field, but also bringing more accurate data back in."
Paper documentation is still used frequently in maintenance
activities. When members of the aircrew show up at the aircraft, they typically
review the paper forms to ensure they know the aircraft's current status. Then,
when they are ready to document their maintenance actions, most technicians
enter the information in electronic form, albeit not until returning to their
duty station where desktop computers are located. "Our future concept is for
maintenance data collection to be completed at the point of maintenance. Using
wireless technology, the data will immediately be updated in the system,"
remarked Breeland. It is anticipated that this practice will be available to
maintenance technicians whether in garrison, deployed to an established forward
base, or when establishing a presence at a bare-base location.
"There can be a maintainer on the flight line, and by the
time he gets back to his shop to put his entries in there, he may have
forgotten what exactly it is he did to take care of the maintenance. Or he may
be in a hurry and make shortcuts, so he doesn't get the same opportunities to
input the same kind of data as could be captured automatically," said Frank
Hale of ARINC, a contractor with the Maintenance Information System cell.
In the future, PMAs may be able to communicate directly with
weapons systems. "Direct connections between PMAs and the equipment being
repaired facilitate rapid analysis of system performance characteristics and
allow faster transfer of critical information for ordering parts, reporting
work performance, and receiving updated technical information," according to a
report carried out by the McLean, VA-based Logistics Management Institute (LMI)
on behalf of the Department of Defense. Current obstacles to such direct
communication include information security concerns - particularly when dealing
with wireless - and bandwidth. Fortunately, because most maintenance information
is sensitive but unclassified, sufficient protection may be available through
COTS products such as data encryptors and virtual private networks.
For wireless operations, advantages include time
savings/instant data access, more accurate and up-to-date data, and more
efficient utilization of personnel, where more people perform direct
maintenance rather than support functions.
Software, of course, is also key to enhancing the efficiency
of maintenance technicians. Snow explained that each piece of equipment has to
be tracked independently and each has a different maintenance history. What one
jet engine may need another one may not, or they may have different attributes
and therefore may require different replacement parts. Mechanics may spend a
lot of time just trying to decipher what it is that they need.
Snow's company develops Enigma 3C, an interactive product
encyclopedia that allows technicians to type in the serial number for a
particular piece of equipment and get access to the most up-to-date service
bulletins and other data that is relevant to that component. "What you start to
find out is that there are anywhere between five and 10 different places that
mechanics typically have to go to find information about how to fix equipment,
which is why they spend so much time looking for information," said Snow. "What
we do is consolidate all that diverse information into a single, integrated
product encyclopedia."
Enhancing Data Mobility
In the Air Force, many major commands and bases have
implemented PMAs. The Air Force has formally sanctioned two
point-of-maintenance test bases, Hurlburt Field, FL, and Nellis Air Force Base,
NV. Testing at Hurlburt Field has focused primarily on development of
point-of-maintenance software to be used on hand-held devices, and testing at Nellis
has centered on use of ruggedized laptop computers.
Twelve AMC bases have fielded wireless technology on their flightlines,
and they are using e-tools to document maintenance. Other bases have fielded,
or are in the process of fielding, point-of-maintenance-type capabilities using
various types of e-tools. All three of the Air Force's air logistics centers
are using e-tools and wireless technology to document various maintenance and
financial actions.
The EDNA device has been used with the F-16, F-117 and B-2
aircraft since the mid-1990s. According to the LMI report, the device appears
to be virtually indispensable for complex diagnostics, operational flight plan
upload, and flight data download. The DataTrak Model 20 has been used with the
F-22.
In the Marine Corps, technicians working on the AH-1W Super
Cobra helicopter have tested a maintenance mentoring system that aids in
troubleshooting and diagnostics, according to LMI. It consists of a ruggedized
tablet-style computer, developed by Intelliworxx Inc., which a maintenance
technician can wear or carry. The primary interface is voice recognition, with
a touch-sensitive screen as a backup. There is a Web browser as well, from
which the technician can access additional information.
The Air Force Research Laboratory has conducted usability
studies of various e-tools including the Xybernaut head-mounted display
wearable computer and wrist-mounted wearable computer. "We anticipate that once
fully tested and found effective by the testing community, widespread use will
be forthcoming," declared Breeland.
Challenges Remain
LMI concluded that before PMAs can be effectively employed
in DoD maintenance environments, several challenges must be addressed. They
include poor readability in sunlight, short battery life, and environmental
factors such as temperature extremes, moisture, corrosion, vibration,
electromagnetic interference and dust, which can seriously degrade the
performance of some PMAs. However, sunlight problems can be overcome with photo
sensor technology, which can enhance readability. Obviously, these are not as
large concerns in the hangar environment compared with the flight line.
However, with wireless communication there can be a slow response time due to
the amount of metal in the hangars. Remedying this requires upgrading wireless
LAN infrastructures.
For portable electronic display devices, other problems have
included the following: touch screens sometimes stopped working, batteries died
quickly, words were sometimes too small on the screens and schematic displays
could be hard to read.
Also, carrying the tablet in a pouch suspended from a strap
around one's neck can be awkward, and the cord connecting a headset to the
tablet is a potential safety hazard. In addition, the pointer used to interface
with the tablet's touch screen can be a source of foreign object damage.
Insufficient integration with existing maintenance
management systems and emerging maintenance automation initiatives have
adversely affected some DoD PMA initiatives as well, such as with the F/A-18E/F
program.
Cultural resistance is another challenge. In the LMI study,
about a quarter of the technicians were initially uncomfortable with computers
and were reluctant to use the EDNA. Researchers found that older technicians
seem more resistant to the technology, while younger ones are less critical of
it. To help overcome cultural obstacles, effective management focus and adequate
user training are essential.
Breeland expects manpower studies conducted in the future to
help quantify specific improvements provided through use of e-tools and new
technology, but currently, the only quantification of performance is done in an
informal, indirect manner (i.e., word of mouth, trip reports, etc.). The
activities are not well enough implemented to warrant the development of an
evaluation program/module. Nevertheless, there can be no doubt that PMAs and ETMs
are revolutionizing the way military aircraft are maintained. |